Quick and Reliable Packaging Machine Fixing Solutions to Minimize Downtime
In the affordable landscape of manufacturing, the efficiency of product packaging operations depends upon the dependability of machinery. Quick and trusted repair service solutions are vital in reducing downtime, which can bring about considerable monetary losses and operational setbacks. Comprehending the importance of timely interventions and the function of expert professionals can transform just how companies approach upkeep and repair work. Nonetheless, navigating the myriad alternatives available for fixing services can be difficult. What factors should services consider to ensure they are making the ideal selection for their operational requirements?
Significance of Timely Fixes
Prompt repair services of product packaging makers are critical for keeping functional performance and lessening downtime. In the hectic atmosphere of production and packaging, even small breakdowns can result in significant delays and performance losses. Addressing concerns without delay makes sure that makers operate at their optimal capacity, therefore securing the circulation of operations.
Moreover, timely and regular upkeep can stop the acceleration of minor troubles right into major breakdowns, which usually sustain higher repair service costs and longer downtimes. A proactive strategy to maker repair work not only maintains the stability of the equipment yet likewise boosts the general reliability of the assembly line.
Furthermore, timely fixings add to the long life of packaging equipment. Makers that are serviced promptly are much less likely to struggle with excessive damage, allowing organizations to maximize their financial investments. This is particularly vital in markets where high-speed product packaging is vital, as the demand for constant efficiency is paramount.
Advantages of Reliable Company
Trustworthy service carriers play a pivotal role in ensuring the smooth operation of packaging devices. Their competence not just improves the effectiveness of repair services yet also contributes considerably to the long life of devices.

In addition, a trusted company offers thorough support, including training and support for staff on equipment procedure and upkeep best practices. This not only equips staff members yet additionally grows a society of safety and security and effectiveness within the organization. In general, the benefits of engaging reputable service suppliers expand beyond immediate repair services, positively affecting the whole functional workflow of product packaging procedures.
Typical Product Packaging Maker Concerns
In the world of packaging operations, various problems can jeopardize the effectiveness and functionality of devices. One prevalent trouble is mechanical failing, often stemming from damage or insufficient maintenance. Components such as belts, motors, and gears may stop working, resulting in failures that stop production. Another usual issue is misalignment, which can cause jams and irregular packaging, influencing item high quality and throughput.
Electric troubles can likewise interrupt product packaging procedures. Malfunctioning read here wiring or malfunctioning sensors may lead to irregular maker habits, triggering delays and enhanced operational costs. Furthermore, software program glitches can prevent the maker's programs, bring about operational inefficiencies.
Irregular product circulation is one more critical issue. This can occur from variations in item dimension, weight, or shape, which may impact the device's capability to deal with products accurately. Inadequate training of operators can exacerbate these issues, as inexperienced workers may not acknowledge very early indicators of breakdown or may abuse the equipment.
Attending to these usual packaging machine concerns without delay is important to keeping efficiency and making certain a smooth procedure. Routine examinations and aggressive upkeep can substantially minimize these concerns, fostering a reputable packaging environment.
Tips for Decreasing Downtime
To decrease downtime in packaging operations, implementing an aggressive upkeep approach is crucial. On a regular basis set up upkeep checks can determine prospective issues prior to they intensify, making certain makers operate effectively. Establishing a regimen that includes lubrication, calibration, and examination of essential components can dramatically minimize the frequency of unforeseen breakdowns.
Training staff to run equipment properly and identify early caution signs of breakdown can also play a vital function. Equipping drivers with the expertise to perform fundamental troubleshooting can avoid small problems from triggering significant hold-ups. Moreover, keeping a well-organized supply of essential extra parts can expedite repair services, as waiting for parts can bring about prolonged downtime.
Additionally, documenting maker efficiency and maintenance tasks can aid determine patterns and persistent issues, permitting targeted treatments. Integrating sophisticated monitoring innovations can supply real-time data, making it possible for anticipating maintenance and minimizing the danger of sudden failings.
Finally, fostering open communication between drivers and maintenance groups ensures that any abnormalities are promptly reported and attended to. By taking these positive actions, organizations can boost operational efficiency and substantially lower downtime in product packaging check my source procedures.
Picking the Right Fixing Solution
Choosing the ideal repair service for packaging machines is a critical decision that can considerably affect operational efficiency. A well-chosen provider makes sure that your equipment is repaired promptly, properly, and to the highest possible standards. Begin by examining the copyright's experience with your specific sort of product packaging devices. A technician acquainted with your machinery can diagnose issues more properly and execute remedies much more rapidly.
Following, take into consideration the solution company's online reputation. Looking for responses from various other companies within your industry can provide understandings into reliability and top quality. Certifications and partnerships with identified devices producers can additionally show a dedication to excellence.
Additionally, assess their reaction time and schedule. A provider who can offer prompt assistance reduces downtime and maintains production circulation stable. It's also vital to ask about warranty and service guarantees, which can show the self-confidence the copyright has in their job.

Final Thought
In final thought, the significance of trustworthy and quick product packaging equipment repair work solutions can not be overstated, as they play a critical role in decreasing downtime and making go to the website certain operational performance. Applying proactive maintenance practices and spending in team training further boosts the long life of packaging equipment.
Prompt repairs of packaging equipments are vital for keeping operational efficiency and reducing downtime.Additionally, timely repair work add to the long life of product packaging equipment. Overall, the benefits of involving reliable service suppliers expand past instant fixings, favorably influencing the whole operational operations of packaging procedures.
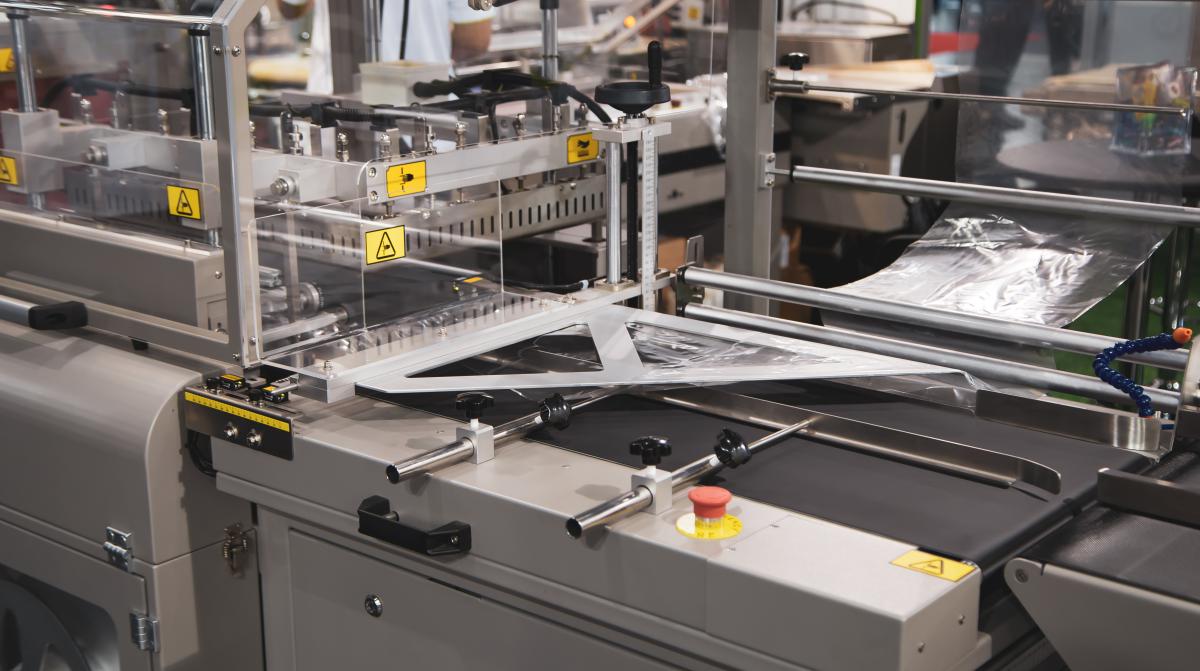